Empower Your Team with the Digital Wrench
AI Agent for Maintenance
Unlock faster, smarter maintenance with our AI-powered Digital Wrench — guiding technicians with real-time audio instructions, automating documentation, and streamlining data access for maximum efficiency.
Enabling Targeted and Efficient Maintenance
Transform Maintenance – From Reactive to Proactive
Experience a paradigm shift in robotics with our Predictive Maintenance feature, a cornerstone for highly available robot fleets.
By leveraging advanced analytics and real-time data, our software anticipates potential issues and enables proactive interventions before equipment failure.
This not only minimizes downtime but also extends the lifespan of robotic assets.Predictive Maintenance optimizes resource allocation through targeted interventions, ensuring that maintenance efforts are directed exactly where they are most urgently needed.
Adopt a cost-effective approach that revolutionizes the efficiency of your robot fleet and transforms maintenance from a reactive duty to a proactive, strategic advantage for sustainable operational excellence.up to
38%
Shorter Mean-Time-To-Repair (MTTR)
Faster repairs minimize downtime, save technician hours and boost efficiency
up to
42%
Longer Mean-Time-Between-Failures (MTBF)
Enhance reliability and save internal and external costs
up to
29%
More On-Site Fixes
Enabled on-site teams reduce costly external dependencies
Unforeseen Possibilities with the Intelligent Maintenance Agent (WAKU IMA)
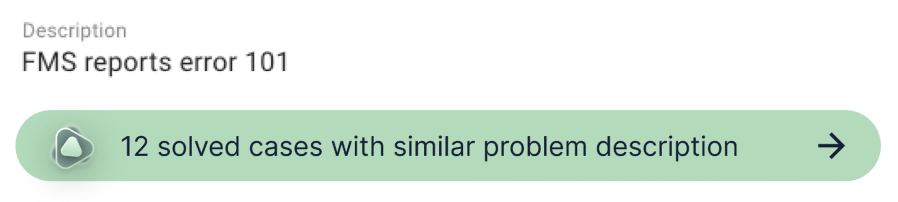
Experience the Full Benefits Now
Customer Voices
WAKU Care plays a crucial role in our support and maintenance strategy. It is an excellent software equipped with numerous AMR-specific and highly intelligent functionalities. This guides our technicians throughout the entire process and enables our customers to monitor their AMR assets seamlessly.
Dr. Andreas Bahke, Vice President Robotics at Körber Business Area Supply Chain
Read Success Storyup to
34%
Less unplanned downtimes
Avoid costly outages and productivity losses by preventive maintenance
up to
28%
Higher Asset Availibility
Maximize operational uptime, boost productivity, and improve overall efficiency
up to
36%
Extended Asset Lifetime
Save costs (CAPEX) for new assets by longer lifecycles
Take action now
Request Demo Session
We will be delighted to show you the performance of WAKU Care. Discover everything that WAKU Care can offer you and your organization. Evaluate the benefits for your needs and receive a customized offer.